AUO Emerges as Early Leader in True MicroLED Display Manufacturing
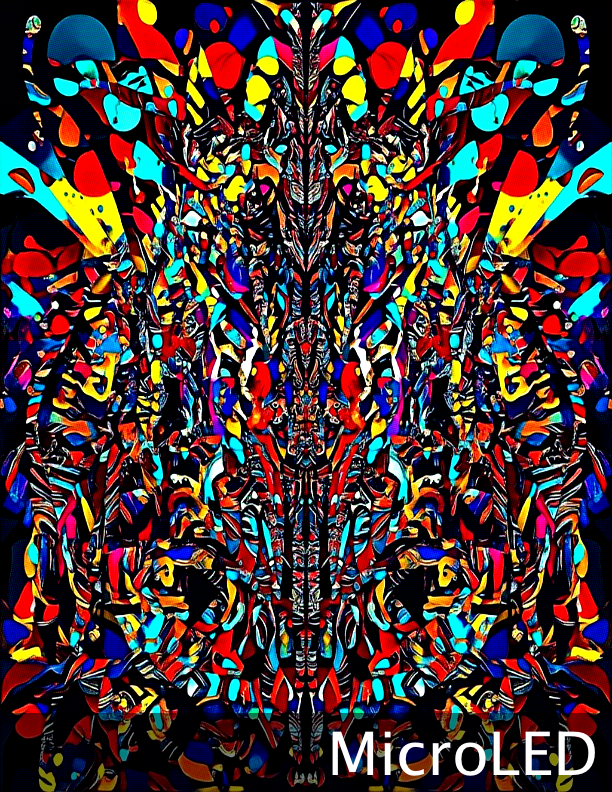
By Dave Haynes
AUO Corporation (AUO) has a well-established position as one of the world’s largest flat panel screen manufacturers, but the Taiwan company has put years into R&D that anticipated microLED would be the next big thing in consumer and commercial displays.
While numerous manufacturers, large and small, have been actively marketing LED video wall products as microLED, they’ve almost all been selling miniLEDs that are micro in marketing name only. AUO is among very few companies actually manufacturing components and displays that meet the most common technical definitions for microLED, which are based around the physical size of the LED light emitters.
If you have seen a display at a trade show that meets those definitions, and display nerds have validated it as being “true” microLED, there’s a very good chance the display was developed by AUO or one of the companies under the company’s big corporate umbrella – as a subsidiary or through substantial investment. For example, the headline-grabbing transparent microLEDs at a Korean brand company’s 2024 CES, ISE and InfoComm trade show stands came out of AUO’s production facilities.
MicroLED represents one of a handful of key initiatives by the Hsinchu company to broaden its business beyond LCD flat panels – driven in part by the increasing challenge of trying to compete with government-subsidized manufacturers across the Taiwan Strait in mainland China.
Along with strengthening a position as the early adopter and market leader in microLED, AUO is also working on several other ways to solidify and build on its longstanding LCD business, and also drive sustainability (ESG) initiatives.
A Decade Of Early Work
“We’ve been developing microLED technology for more than 10 years,” says Kevin Guo, Director of the smart retail business unit for AUO Display Plus.
Display Plus operates as AUO’s subsidiary, using the parent company’s manufacturing capabilities but maintaining its own business focus. During a week of interviews last fall in Taiwan, the footprint and business tentacles of AUO were obvious, with numerous companies revealing in presentations that AUO had ownership positions or other substantial business ties.
Based in the same sprawling, ultra-modern science park as global semiconductor giant TSMC, AUO manufactures TVs and commercial displays for many of the world’s top brands. Where other display manufacturers directly sell displays under their brand(s), AUO is a white-label manufacturer that sells components or finished displays to other manufacturers, who then apply their branding.
AUO has also been broadening its scope beyond display hardware – acquiring a series of digital signage software companies than can leverage AUO manufacturing for the displays, but also provide a management platform. Those companies include the U.S. firms ComQi, Rise Vision and John Ryan (through ComQi), and the Taiwan firm Space4M. The U.S. collaboration display tech firm Avocor was also acquired in Q3 2024.
Three Main Focus Areas For MicroLED
There are three main focus areas for AUO’s work in microLED and what it calls custom electronics: large format displays like TVs and commercial panels, wearable devices and a variety of display applications for the auto sector. Watches, so far, are the most commercially advanced, with a top European luxury timepiece brand expected to launch a product with a microLED face some time in 2025.
That watch has a 1.39” face that packs in 326 pixels per inch, using microLED light emitters smaller than 30 micrometers. The primary advantage over OLED timepiece displays is brightness, with this watch capable of a fully daylight-readable 3,000 nits, though normal mode is 1,000 nits.
AUO has been showing microLED prototypes since 2018, starting with an eight-inch display that has 169 pixels per inch. Sizes, form factors and capabilities have broadened as R&D continued and by 2023, AUO was able to provide microLED modules that were tiled vertically and horizontally to produce an 89-inch “true” microLED TV, branded by AUO’s Korean customer.
Since then, AUO has also introduced 76, 101 and 114-inch models and large form-factor transparent microLED displays at trade shows, directly and via electronics brands.
Its technology uses 0.6 and 0.7mm pixel pitches and LTPS backplanes, and two different display module sizes – 12.7″ and 16.1″ – that allow panels to be tiled to realize various display configurations. Like more conventional, modular LED displays, adding more modules horizontally and vertically produces incrementally larger finished displays.
AUO also demonstrated in 2024 a 31-inch single module, using active matrix technology – billed as the world’s largest single piece module for microLED. It takes just 12 of those modules, tiled together, to make a 108” diagonal display. Larger modules mean faster assembly, fewer seams, fewer driver integrated circuits and faster production time. Most of those factors help lower costs. Active matrix, by the way, is a type of display technology that uses a grid of transistors to control each pixel, resulting in better image quality and faster response times than possible using passive matrix technology.
Better Than OLED
AUO positions microLED as its future display technology, because it has lower capital requirements when compared to OLED manufacturing, and greater flexibility in scaling production up and down.
The technology offers several key advantages including transparency, form factor flexibility, seamless tiling capability, high reliability, longer operating life, superior HDR performance, and wide viewing angles.
AUO also suggests microLED offers much more manufacturing flexibility, and a substantially lower barrier to entry. “Right now, if you want to invest one OLED fab, you need to invest more than several billion US. That’s huge money to prepare one fab, especially when you don’t have national government support, like in China,” explains Ivan Wu, VP for Display Product R&D. “So we start the microLED investment, with less capital, and we can scale up very flexibly, based on business planning.”
Wu says AUO’s target is getting microLED at cost-parity by 2030, reducing costs by 50% every two years to get there.
Getting Competitive
Reaching cost parity with OLED involves several factors:
- Reducing the bill of materials cost;
- Improving panel performance;
- Improving yield rates, the ideally very high percentage of working vs dead pixels during manufacturing.
One of the ways to reduce component costs is minimizing the use of third parties and instead working with companies that are in the corporate family, in some fashion. The microLED die, for example, come from two other Taiwan companies, Ennostar (an AUO group company) and PlayNitride, which has AUO as its second-largest shareholder.
There is also a drive to reduce the already tiny size of microLED lights, which are “grown” on semiconductor wafers. More die per wafer means more efficient manufacturing. Along the same lines, modules even larger than 31-inch are being explored to reduce manufacturing and assembly costs.
R&D is also working with partners like Raydium and BHTC on ways to boost the microLED light efficiency by working with the circuitry and finding ways to enhance the light.
“We have a lot of equipment vendors cooperating with each other,” relates Wu, “to enlarge the size, looking at how to improve the accuracy and how to improve the (produced) units per hour, to improve the mass transfer efficiency, many things.”
MicroLED Plays With Conventions
When I visited AUO at its main offices, about an hour south of Taipei in bustling, tech-centric Hsinchu, my hosts walked me through a formal demo center and also though an ad hoc one set up with R&D product.
Among the displays:
- A series of smaller microLED displays intended for auto dashboards and related in vehicle displays;
- A 60-inch version of a transparent microLED with 0.7mm pitch and roughly 60% transparency;
- A slot machine prototype – using what AUO calls a Real Depth 3D Display – that has a tiled 30-inch microLED array as the front glass and then a 300 nit LCD with anti-reflective tech 20mm behind it, creating the illusion of depth and dimension;
- A 17.3-inch transparent microLED that carries the name Rapid Black Switchable, because the 0.3mm pitch display has a dynamic transparency adjustment feature built-in. If ambient lighting gets brighter – perhaps from conditions outside – the display adds shading to boost contrast and improve viewability. AUO says this is something transparent OLED can’t do, and sees applications for auto, as dynamic side windows.
Core LCD Products Still Viable
While R&D direction has focused a lot on next-generation technology like microLED, AUO and AUO Display Plus still see a lot of business opportunity for the mainstream display format that drives most of its current revenues – LCD.
The company’s showroom has a wide variety of demonstration products and contextual scenes for different use-cases like retail, health care and mass transport.
While LED has supplanted even narrow-bezel LCD for video wall projects, there are still lots of high-volume applications for information displays for market segments like airports and quick service restaurants.
Something that sets AUO apart from more familiar display electronics is the ability to manufacture unusual and custom shapes. The showroom includes a crisp, round LCD and a series of ribbon displays in a variety of dimensions. The skinniest are designed to occupy the front of store shelves as full color and dynamic alternatives to electronic shelf labels, while larger versions are finding their way into retail projects as headers over shelves and endcaps, and as wide but short displays that can be attached to the ceilings of subway and passenger rail cars.
When these “bar-type” and other custom LCD display shapes first came on the market, they tended to be larger displays that were manually cut and then re-manufactured to a new dimension, which added cost and could affect build quality.
Now AUO “natively” makes the displays in these dimensions, and can efficiently do relatively small (by TV manufacturing standards) production runs.
Early Days Still
While product is starting to get into the hands of customers, AUO stresses these are still very early days for microLED display.
From a manufacturing point of view, says Wu, “we are still in the beginning stage. We are preparing a next generation production line, and we believe we will have the capability to be better than our competitors.”
So who are those competitors?
“We stand out from our competitors,” says Wu, “because the others, they’re just preparing demo samples. But we’re delivering formal modules to our customers. So that’s very different.”
“All of the major players are developing microLED, we see that,” adds Hank Liu, a longtime AUO executive who oversees digital signage business, “but we are the fastest in this race, so far.”
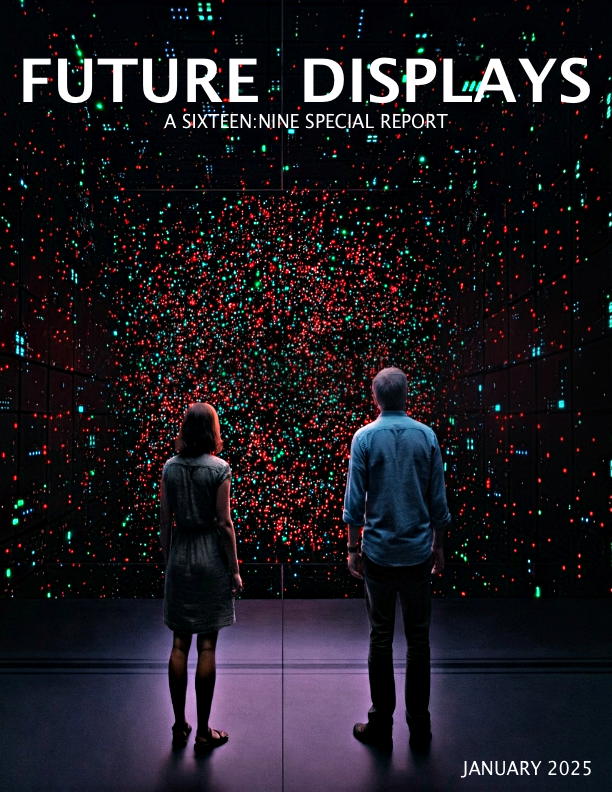